כיצד לעצב חלקי פלסטיק
תיאור קצר:
ל לעצב חלקי פלסטיקזה להגדיר את הצורה, הגודל והדיוק של החלקים, בהתבסס על התפקיד שממלאים החלקים במוצר, וכלל תהליך העיצוב של הפלסטיק. התפוקה הסופית היא שרטוטים לייצור עובש וחלק הפלסטיק.
ייצור מוצרים מתחיל בתכנון. תכנון חלקי הפלסטיק קובע ישירות את מימוש המבנה הפנימי, עלותו ותפקודו של המוצר, וקובע גם את השלב הבא של ייצור עובש, עלות ומחזור, כמו גם את תהליך ההזרקה והעלייה לאחר העיבוד.
חלקי פלסטיק נמצאים בשימוש נרחב במוצרים שונים, מתקנים וחיי אנשים בחברה המודרנית. חלקי פלסטיק דורשים צורות ופונקציות שונות. הם משתמשים בחומרים פלסטיים ותכונותיהם מגוונות. יחד עם זאת, ישנן דרכים רבות לייצר חלקי פלסטיק בתעשייה. אז לעצב חלקי פלסטיק זו לא עבודה פשוטה.
עיצוב וחומר חלקים שונים מיוצרים בעיבודים שונים. העיבוד ליצירת פלסטיק כולל בעיקר להלן:
1. הזרקת דפוס
2. דפוס נושבת
3. דפוס דחיסה
4. דפוס סיבובי
5. טיפול אחר
6. שחול
7. ייצור
8. קצף
ישנן דרכים רבות לייצר אותן באופן המוני. הזרקה היא שיטת ייצור פופולרית, מכיוון שהזרקת 50% ~ 60% חלקי פלסטיק מיוצרים על ידי הזרקת הזרקה, זוהי יכולת ייצור במהירות גבוהה.
הציגו חלונות עבור חלקי פלסטיק שתכננו:
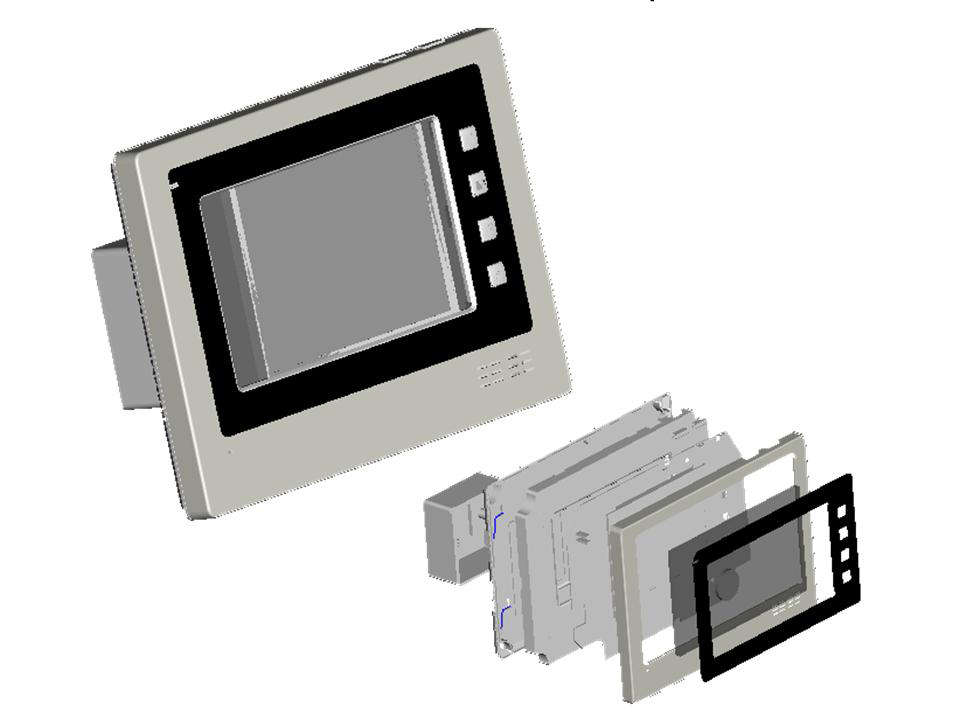
מארז פלסטיק של טלפון חזון
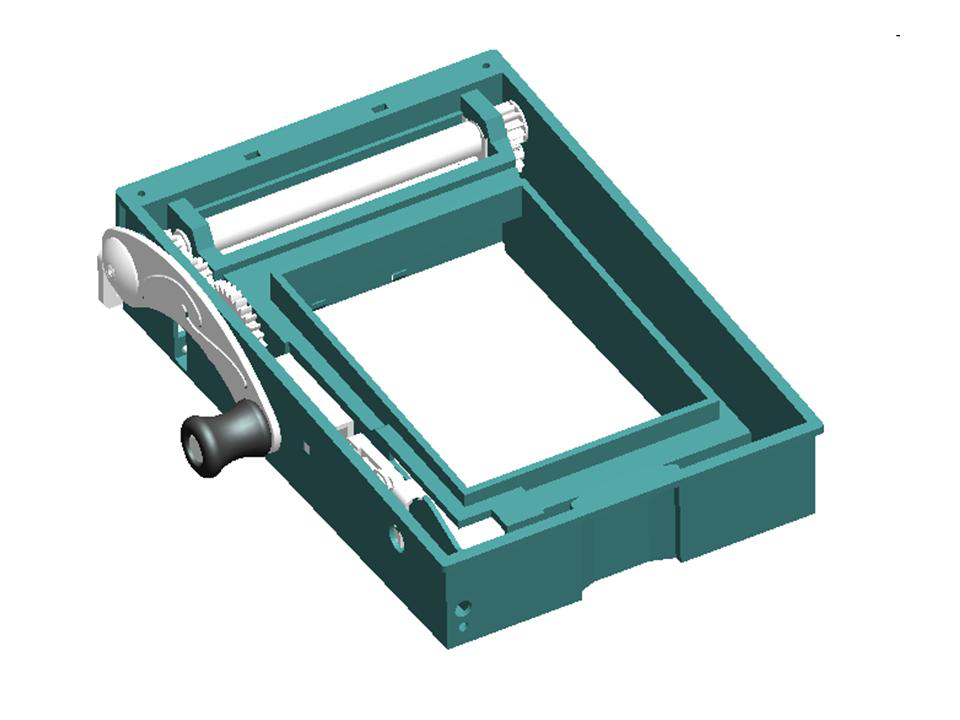
חלקי פלסטיק של מנגנון
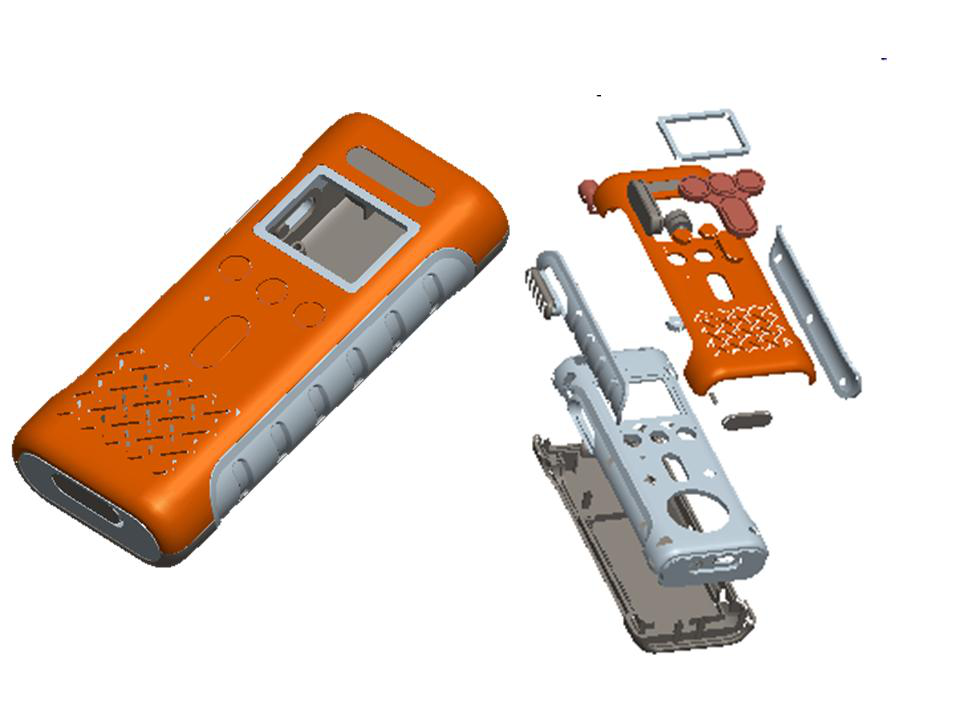
מארזי פלסטיק של אלקטרוניקה
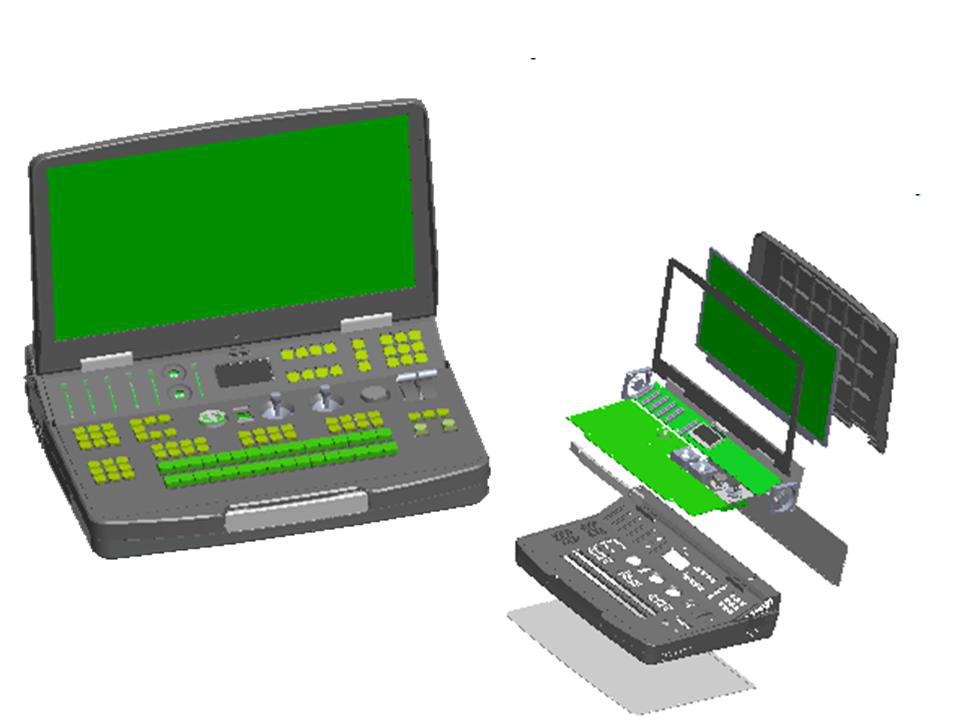
בית פלסטיק למכשיר
להלן אנו משתפים בפירוט כיצד לעצב חלקי פלסטיק בשלושה היבטים
* 10 טיפים לעיצוב חלקי פלסטיק שאתם חייבים להכיר
1. קבעו את עיצוב המראה וגודל המוצר.
זהו השלב הראשון בכל תהליך העיצוב. על פי מחקרי שוק ודרישות הלקוח, קבעו את המראה והתפקוד של המוצרים וגיבשו משימות לפיתוח מוצרים.
על פי משימת הפיתוח, צוות הפיתוח ממשיך את ניתוח ההיתכנות הטכנית והטכנולוגית למוצר, ובונה את מודל המראה התלת ממדי של המוצר. ואז, על פי מימוש פונקציות והרכבת מוצרים, מתוכננים חלקים אפשריים.
2. הפרד חלקים בודדים מציורי מוצר, בחר סוג שרף פלסטיק לחלקי פלסטיק
שלב זה הוא להפריד בין החלקים לבין מודל התלת מימד שהושג בשלב הקודם ולעצב אותם כפרטיים. על פי הדרישות הפונקציונליות של החלקים, בחרו חומרי גלם פלסטיים או חומרי חומרה מתאימים. לדוגמה, ABS משמש בדרך כלל ב-
מעטפת, ABS / BC או PC נדרשת לתכונות מכניות מסוימות, חלקים שקופים כגון אהיל, מנורת PMMA או PC, ציוד או חלקי ללבוש POM או ניילון.
לאחר בחירת חומר החלקים, ניתן להתחיל בעיצוב הפרטים.
3. הגדר זוויות טיוטה
זוויות טיוטה מאפשרות הוצאת הפלסטיק מהתבנית. ללא זוויות טיוטה, החלק יציע עמידות משמעותית עקב חיכוך במהלך ההסרה. זוויות טיוטה צריכות להיות נוכחות בחלק הפנימי והחיצוני של החלק. ככל שהחלק עמוק יותר, כך זווית הטיוטה גדולה יותר. כלל אצבע פשוט הוא שתהיה זווית גרירה של מעלה אחת לאינץ '. אי-זווית גרירה מספקת עלולה לגרום לשריטות בצידי החלק ו / או לסימני סיכה מפליטה גדולה (על כך בהמשך).
זוויות טיוטה של המשטח החיצוני: ככל שהחלק עמוק יותר, כך זווית הטיוטה גדולה יותר. כלל אצבע פשוט הוא שתהיה זווית גרירה של מעלה אחת לאינץ '. אי-זווית גרירה מספקת עלולה לגרום לשריטות בצידי החלק ו / או לסימני סיכה מפליטה גדולה (על כך בהמשך).
בדרך כלל, על מנת להיות בעל מראה טוב למראה, המרקם נוצר על פני החלקים. הקיר בעל המרקם הוא מחוספס, החיכוך גדול, ולא קל להסיר אותו מהחלל, ולכן הוא דורש זווית ציור גדולה יותר. המרקם הגס יותר הוא, דרושה זווית שרטוט גדולה יותר.
4. הגדר עובי דופן / עובי אחיד
יציקת צורה מוצקה אינה רצויה בהזרקה בגלל הסיבות הבאות:
1) זמן הקירור הוא פרופורציונלי לריבוע עובי הקיר. זמן קירור ארוך למוצק יביס את כלכלת הייצור ההמוני. (מוליך חום גרוע)
2). קטע עבה יותר מתכווץ מקטע דק יותר, ובכך מציג התכווצות דיפרנציאלית וכתוצאה מכך עמוד עיוות או כיור וכו '(מאפייני הצטמקות של פלסטיק ומאפייני pvT)
לכן יש לנו כלל בסיסי לעיצוב חלקי פלסטיק; עד כמה שאפשר עובי הקיר צריך להיות אחיד או קבוע לאורך החלק. עובי דופן זה נקרא עובי דופן נומינלי.
אם יש חלק חלק כלשהו בחלק, יש להפוך אותו לחלול על ידי הכנסת ליבה. זה אמור להבטיח עובי דופן אחיד סביב הליבה.
3). מה השיקולים להחלטת עובי הקיר?
עליו להיות עבה ונוקשה מספיק לתפקיד. עובי הקיר יכול להיות 0.5 עד 5 מ"מ.
זה גם חייב להיות דק מספיק כדי להתקרר מהר יותר, וכתוצאה מכך משקל חלק נמוך יותר ופרודוקטיביות גבוהה יותר.
יש לשמור על כל שינוי בעובי הקיר במינימום האפשרי.
חלק מפלסטיק בעובי דופן משתנה יחווה קצב קירור שונה והתכווצות שונה. במקרה כזה השגת סובלנות קרובה הופכת להיות קשה מאוד ופעמים רבות בלתי אפשרית. כאשר וריאציה בעובי הקיר היא חיונית, המעבר בין השניים צריך להיות הדרגתי.
5. עיצוב חיבור בין חלקים
בדרך כלל עלינו לחבר שני קליפות יחד. כדי ליצור חדר סגור ביניהם להצבת הרכיבים הפנימיים (מכלול PCB או מנגנון).
סוגי החיבורים הרגילים:
1). ווים מצמידים:
חיבור ווים הצמד משמש בדרך כלל במוצרים קטנים ובינוניים. המאפיין שלה הוא שקרסוליות נקבעים בדרך כלל בקצה החלקים, וניתן להקטין את גודל המוצר. כשהוא מורכב, הוא נסגר ישירות מבלי להשתמש בכלים כמו מברג, מתכת לריתוך קולי ואחרים. החיסרון הוא שקרס ההצמדה עלולים לגרום לעובש מסובך יותר. יש צורך במנגנון המחוון ובמנגנון ההרמה בכדי לממש את חיבור וו ההצמדה ולהגדיל את עלות התבנית.
2). מפרקי בורג:
מפרקי הברגים יציבים ואמינים. בפרט, קיבוע הבורג + האומים הוא אמין ועמיד מאוד, ומאפשר פירוקים מרובים ללא סדקים. חיבור הבורג מתאים למוצרים בעלי כוח נעילה גדול ופירוק מרובה. החיסרון הוא שעמוד הבורג תופס יותר מקום.
3). בוסי הרכבה:
חיבור הבוסים ההרכבה הוא לתקן שני חלקים על ידי תיאום הדוק בין הבוסים לחורים. דרך חיבור זו אינה חזקה דיה בכדי לאפשר מוצרי פירוק. החיסרון הוא שכוח הנעילה יקטן ככל שזמן הפירוק יגדל.
4). ריתוך קולי:
ריתוך אולטרסאונד הוא על ידי הכנסת שני החלקים לתבנית הקולי והתמזגות משטח המגע תחת פעולת מכונת ריתוך קולי. גודל המוצר יכול להיות קטן יותר, תבנית ההזרקה פשוטה יחסית, והחיבור יציב. החיסרון הוא השימוש בתבנית קולי ומכונת ריתוך קולי, גודל המוצר לא יכול להיות גדול מדי. לאחר הפירוק, לא ניתן להשתמש שוב בחלקים הקולי.
6. חתכים
חתכים הם פריטים המפריעים להסרת מחצית התבנית. חתכים יכולים להופיע כמעט בכל מקום בעיצוב. אלה לא מקובלים באותה מידה, אם לא גרוע יותר מהיעדר זווית טיוטה מצדך. עם זאת, חלק מההתחייבויות נחוצים ו / או בלתי נמנעים. במקרים אלה, הכרחי
חתכים מיוצרים על ידי החלקות / נעים בתבנית.
יש לזכור כי יצירת חתכים היא יקרה יותר בייצור התבנית ויש להקפיד על מינימום.
7. תמיכה בצלעות / גסטיות
צלעות בחלק הפלסטי משפרות את הנוקשות (הקשר בין העומס והסטת החלק) של החלק ומגבירות את הנוקשות. זה גם משפר את יכולת העובש כאשר הם מזרזים את זרימת ההיתוך לכיוון הצלע.
צלעות ממוקמות בכיוון של מתח וסטייה מרביים על משטחים שאינם מופיעים בחלק. מילוי עובש, כיווץ ופליטה אמור להשפיע גם על החלטות הצבת הצלעות.
צלעות שאינן מתחברות לקיר אנכי אינן צריכות להסתיים בפתאומיות. מעבר הדרגתי לדופן נומינלית אמור להפחית את הסיכון לריכוז מתח.
צלע - מידות
הצלעות צריכות להיות בעלות המידות הבאות.
עובי הצלעות צריך להיות בין 0.5 ל 0.6 פעמים עובי הקיר הנומינלי כדי למנוע סימן כיור.
גובה הצלעות צריך להיות פי 2.5 עד 3 עובי דופן סמלי.
צלעות צריכות להיות בעלות זווית טיוטה של 0.5 עד 1.5 מעלות כדי להקל על הפליטה.
בסיס הצלעות צריך להיות ברדיוס 0.25 עד 0.4 פעמים עובי הקיר הנומינלי.
המרחק בין שתי צלעות צריך להיות פי 2 עד 3 עובי דופן סמלי פי שניים (או יותר).
8. קצוות משוחררים
כששני משטחים נפגשים, הוא יוצר פינה. בפינה עובי הקיר גדל פי 1.4 מעובי הקיר הנומינלי. התוצאה היא התכווצות דיפרנציאלית ומתח מעוצב וזמן קירור ארוך יותר. לכן, הסיכון לכשל בשירות עולה בפינות חדות.
כדי לפתור בעיה זו, יש להחליק את הפינות ברדיוס. יש לספק רדיוס חיצונית וגם פנימית. לעולם אין פינה חדה פנימית מכיוון שהיא מקדמת סדק. הרדיוס צריך להיות כזה שיאשרו לכלל עובי דופן קבוע. עדיף שיהיה רדיוס פי 0.6 עד 0.75 עובי הקיר בפינות. לעולם אין פינה חדה פנימית מכיוון שהיא מקדמת סדק.
9. עיצוב בוס הברגים
אנו תמיד משתמשים בברגים כדי לתקן שני חצאי מקרים יחד, או להדק PCBA או רכיבים אחרים על חלקי הפלסטיק. כך שבוסי הברגים הם מבנה ההברגה לחלקים וקבועים.
בורג הבורג הוא בעל צורה גלילית. הבוס יכול להיות מקושר בבסיס עם החלק האם או שהוא יכול להיות מקושר בצד. קישור בצד עלול לגרום לחלק עבה של פלסטיק, שאינו רצוי מכיוון שהוא יכול לגרום לסימון הכיור ולהגדיל את זמן הקירור. ניתן לפתור בעיה זו על ידי קישור הבוס דרך צלע לקיר הצדדי כפי שמוצג בשרטוט. ניתן להפוך את הבוס לקשיח על ידי מתן צלעות תומכות.
בורג משמש לבוס כדי להדק חלק אחר. יש סוג הברגים המרכיב חוטים וברגי חיתוך הדריכה. ברגים ליצירת חוטים משמשים על תרמופלסטיים וברגים לחיתוך חוטים משמשים בחלקי פלסטיק תרמוסטיים לא אלסטיים.
ברגים ליצירת חוטים מייצרים חוטים נקביים על הקיר הפנימי של הבוס בזרימה קרה - פלסטיק מעוות במקום ולא נחתך.
על בורג הבורג להיות בעל מידות מתאימות כדי לעמוד בכוחות החדרת בורג והעומס המונח על הבורג בשירות.
גודל הקידוח ביחס לבורג הוא קריטי לעמידות בפני הפשטת הברגה ושליפת הברגים.
הקוטר החיצוני של הבוס צריך להיות גדול מספיק כדי לעמוד בלחץ חישוק עקב היווצרות חוט.
לשעמם יש קוטר מעט גדול יותר בפגרת הכניסה לאורך קצר. זה עוזר באיתור בורג לפני נסיעה פנימה. זה גם מפחית לחצים בקצה הפתוח של הבוס.
יצרני פולימרים נותנים הנחיות לקביעת ממד הבוס לחומרים שלהם. יצרני הברגים נותנים הנחיות לגודל הקידוח הנכון לבורג.
יש להקפיד על חיבורי ריתוך חזקים סביב קידוח הבורג בבוס.
יש לנקוט בזהירות כדי למנוע מתח יצוק בבוס מכיוון שהוא עלול להיכשל בסביבה התוקפנית.
השעמום בבוס צריך להיות עמוק יותר מעומק החוט.
10. קישוט פני השטח
לפעמים, על מנת לקבל מראה נאה, אנו לעיתים קרובות עושים טיפול מיוחד על פני מארז הפלסטיק.
כגון: מרקם, מבריק גבוה, צביעת ריסוס, חריטת לייזר, הטבעה חמה, גלוון וכן הלאה. יש לקחת בחשבון בעיצוב המוצר מראש, כדי למנוע את העיבוד הבא לא ניתן להשיג או שינויים בגודל המשפיעים על הרכבת המוצר.